Within today's fast-paced manufacturing landscape, businesses are continuously looking for methods to improve effectiveness and minimize lead periods. One of some of the transformative solutions gaining momentum is accelerated injection molding. Such an innovative approach not only speeds up the manufacturing process and enables companies to adapt rapidly to changing market needs. With fast injection molding, businesses can produce high-quality prototypes and end-use parts with remarkable speed, opening the way for smoother operations and enhanced competitiveness.
The significance of rapid injection molding extends beyond mere speed. It provides a unique benefit by allowing companies to evaluate and refine their designs in a budget-friendly manner while significantly reducing the dangers inherent to product development. Consequently, manufacturers can optimize their entire production processes, reduce the timeline to launch, and ultimately boost customer satisfaction. Adopting rapid injection molding could very well be the solution to unlocking new levels of productivity in your production journey.
Benefits of Rapid Injection Molding
Fast injection forming offers multiple advantages that noticeably boost the efficiency of goods production. One of the most remarkable advantages is the reduced lead time for prototypes and manufacturing cycles. Traditional injectable molding can be labor-intensive, often taking several weeks or even an extended period to create forms and finish components. In contrast, rapid injection forming can streamline this process, allowing manufacturers to generate usable samples swiftly. This speedy schedule enables businesses to evaluate and refine their prototypes more successfully, ultimately leading to more rapid time to market.
Another important advantage is cost-effectiveness. Fast injection forming utilizes advanced techniques and substances that lower the overall costs of production. By reducing the time and resources needed for form production, producers can achieve reduced unit prices, especially for brief to intermediate manufacturing cycles. This means that businesses can create premium parts without the cost implications that ordinarily comes with traditional practices. The ability to make modifications easily during the manufacturing process also helps with cutting down on spoilage and reducing costs.
Rapid injectable molding also enhances design flexibility. With this approach, producers can test with different styles and substances without significant risk. The quick turnaround on forms allows groups to iterate swiftly and implement feedback from evaluation stages. This flexibility is crucial in today’s fast-paced market, where consumer preferences can evolve quickly. By adopting quick injection forming, companies can tailor their goods to meet evolving needs, giving them a market advantage in their individual industries.
Key Technological Advances in Rapid Injection Molding
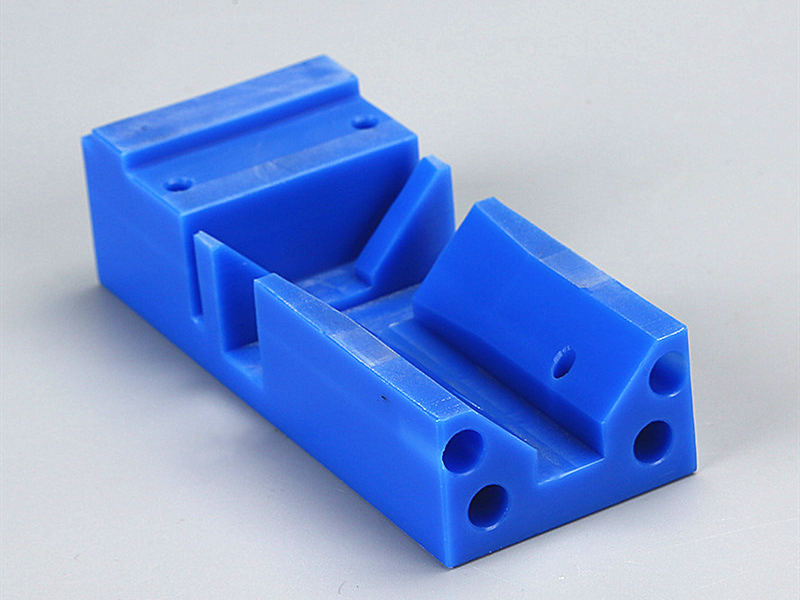
Rapid injection molding employs advanced technologies to improve efficiency and shorten lead times in product manufacturing. One of the fundamental technologies involved is CAD, which enables engineers to create detailed 3D models of components. This accurate modeling helps in discovering potential design flaws at an early stage in the process, enabling rapid modifications that can be executed before moving to production. The combination of CAD software with injection molding machines facilitates a more efficient workflow, ensuring that designs are accurately converted into physical parts.
A further, crucial technology in rapid injection molding is the use of specific materials and additives that improve production speed without compromising quality. High-performance thermoplastics, elastomers, and composites are employed in the molding process, each providing unique properties to meet specific application requirements. Furthermore, the incorporation of cutting-edge polymer blends can enhance the mechanical strength and aesthetic qualities of the finished products. These materials are often engineered to reduce cycle times, allowing manufacturers to produce parts more quickly.
In conclusion, automation and robotic systems play an integral role in streamlining the rapid injection molding process. Mechanized systems can handle part removal, quality inspection, and assembly tasks, thereby reduce manual labor and human error. Robotics also allow faster cycle times and can operate continuously, increasing overall productivity. The combination of these technologies ensures that manufacturers can swiftly respond to market demands while upholding high standards of quality and precision in their products.
Case Studies: Success Stories in the Industry
In the intensely competitive world of electronic goods, a leading smartphone manufacturer turned to quick injection molding to expedite the development of a fresh product line. By employing this cutting-edge technique, they significantly reduced the time from design concept to market launch. The rapid prototyping process allowed for quick iterations and modifications, leading to a conclusive product that not only met market needs but also enabled the company to secure market share ahead of rivals.
A well-known automotive parts supplier faced issues with production delays and escalating costs. By utilizing rapid injection molding, they optimized their manufacturing process and improved product quality. This approach allowed for reduced cycle times and enhanced flexibility in production, resulting in a cut of both time and resources. The manufacturer reported an boosted output and a considerable reduction in time for market entry for new automotive components.
In the healthcare device sector, a startup efficiently leveraged rapid injection molding to bring an novel device to market. The startup was able to partner with their design team to create several prototypes quickly, testing them for functionality and user experience. This streamlined method not only hastened the development process but also allowed them to focus on regulatory compliance, ultimately leading to successful introduction to the market within months rather than years.